Welcome to Australian Wool Innovation, a hub for the woolgrowers of Australia.
Not a woolgrower? Looking for information about wool products, wool care or wool processing?
The Woolmark Company is the global authority on wool. Visit Woolmark.com instead.
Flock to Baggy Green
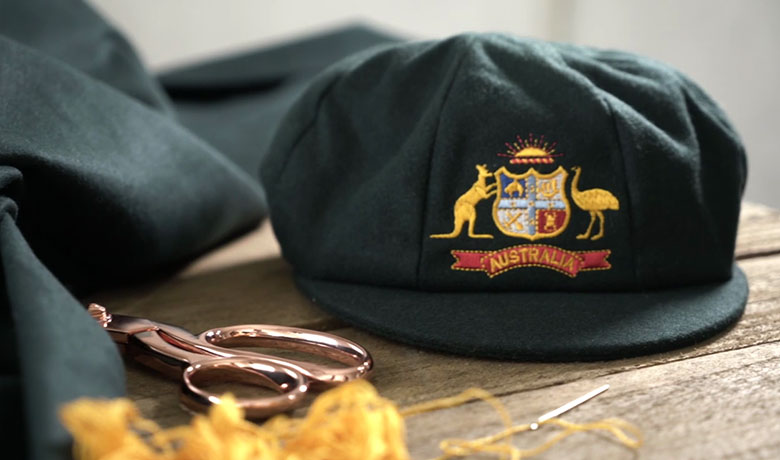
The Flock to Baggy Green was a unique project that combined the Australian wool industry through The Woolmark Company, Cricket Australia and Kookaburra to create special baggy green cloth made from wool donated from right across Australia.
Australian woolgrowers were invited to donate some of their wool to help create the next batch of Baggy Green caps as part of The Flock to Baggy Green project.
In total, just more than 400 woolgrowers have donated wool to the project and the total volume has come to about 500 kilograms. That is enough wool to cap the next 100 years of Australian Test cricketers in donated Australian wool.
The History of Cricket & The Wool Industry
Cricket clubs have long formed a vital part of the fabric of rural communities, with sheep stations many years ago having their own cricket teams and many cricketing heroes past and present having had connections to the wool industry.
Cricket is Australia’s number one participation sport, with an increasing number of Australians enjoying the various forms of the game from backyards to the mighty MCG. The Australian wool industry and cricket have a long association.
The Baggy Green is a proud symbol of Australian cricket, and it is wonderful to have a project that gives woolgrowers from across the country the opportunity to donate some of their wool and be able to trace it to the caps that will be worn by Australian cricketers for years to come.
- James Sutherland, Cricket Australia CEO
The Australian Cricket Coat of Arms, created before Australia officially existed, features a sheep, which shows the wool industry’s prominence in the Australian community when the team first formed.
The Australian Cricket team first wore their woollen Baggy Greens when it sailed for England in 1899. Not surprisingly it was our most significant industry with 25 sheep for every man, woman and child in the colonies. It was fitting the team was captained by Joe Darling; a tough middle order batsman, and South Australian woolgrower.
Wool Donors
Cricket-loving woolgrowers from the outback to the coast, from large pastoral holdings to small family businesses have all answered the call to help grow the Baggy Green.
"We know that the members of Australia’s Cricket team are proud of their baggy green caps but now we hope that when they wear the cap they feel the support of the woolgrowers of Australia."
- Robert & Heather Worner, RC Worner & Co., Wombat NSW
All have donated some of the natural fibre they grow with passion to help make our most sacred sporting icon.
Journey of The Baggy Green
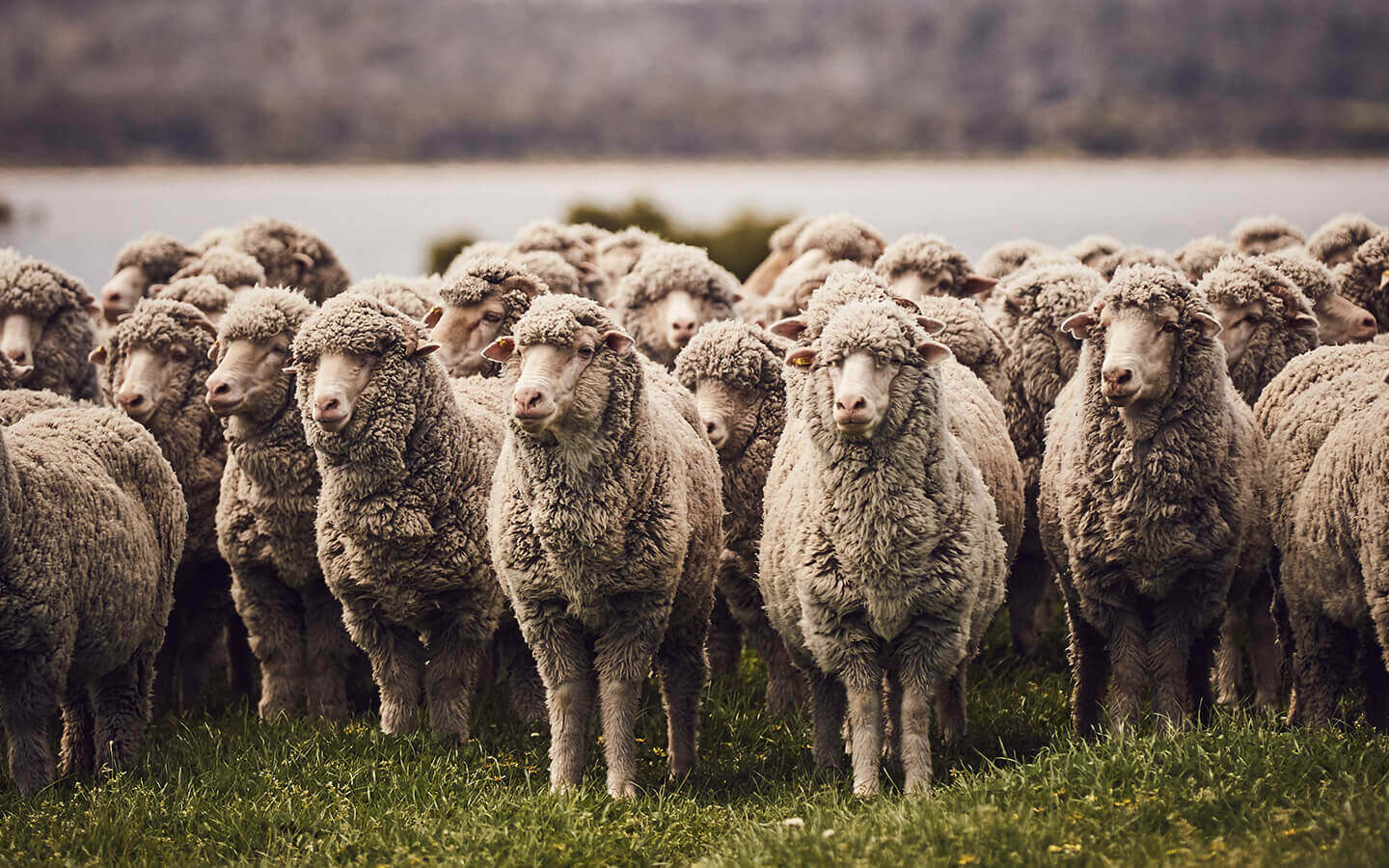
SHEEP
More than 400 woolgrowers from across Australia donated a sample – some a handful, some a whole bale – to the Flock to Baggy Green project. From the finest Merino to a handful of 27-micron wool, the donations filled the wool pack of the Flock to Baggy Green project. Together these donations were processed to create one long run of fabric to make the iconic Australian cricketers Baggy Green.
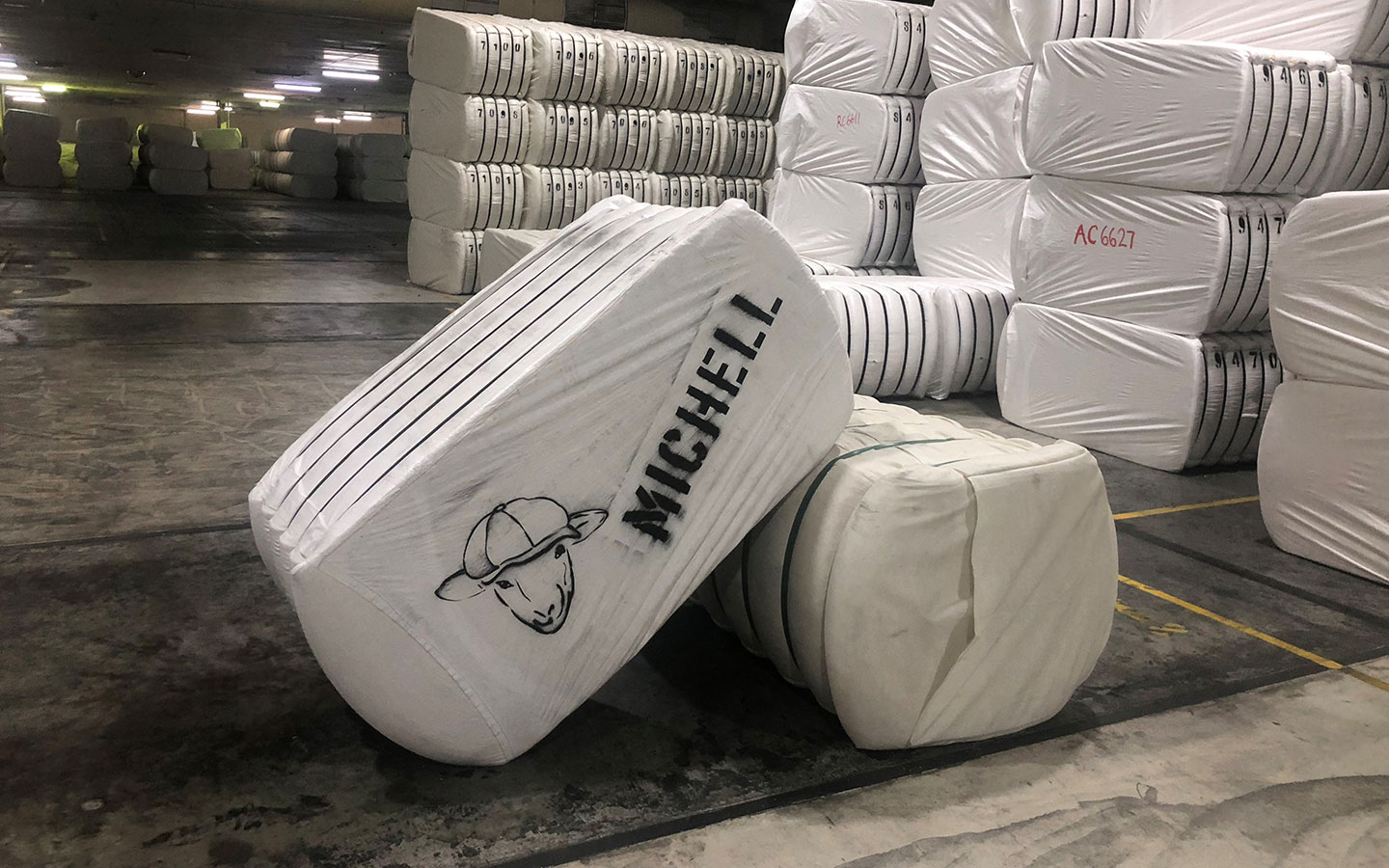
SCOURING
Australian mill and manufacturer Michell Wool took the donations for the first stage of processing.
Scouring the wool involved the greasy wool being fed into a machine where it was continuously transported through a series of bowls, typically between 6 and 8 bowls, containing wash liquor. In the initial two to three wash bowls the wash liquors comprise warm water, containing detergent and sometimes an alkali, to remove most of the wool grease. The remaining bowls contained fresh water to thoroughly rinse the wool.
The wool was then ready for the next stage of manufacturing known as top-making.
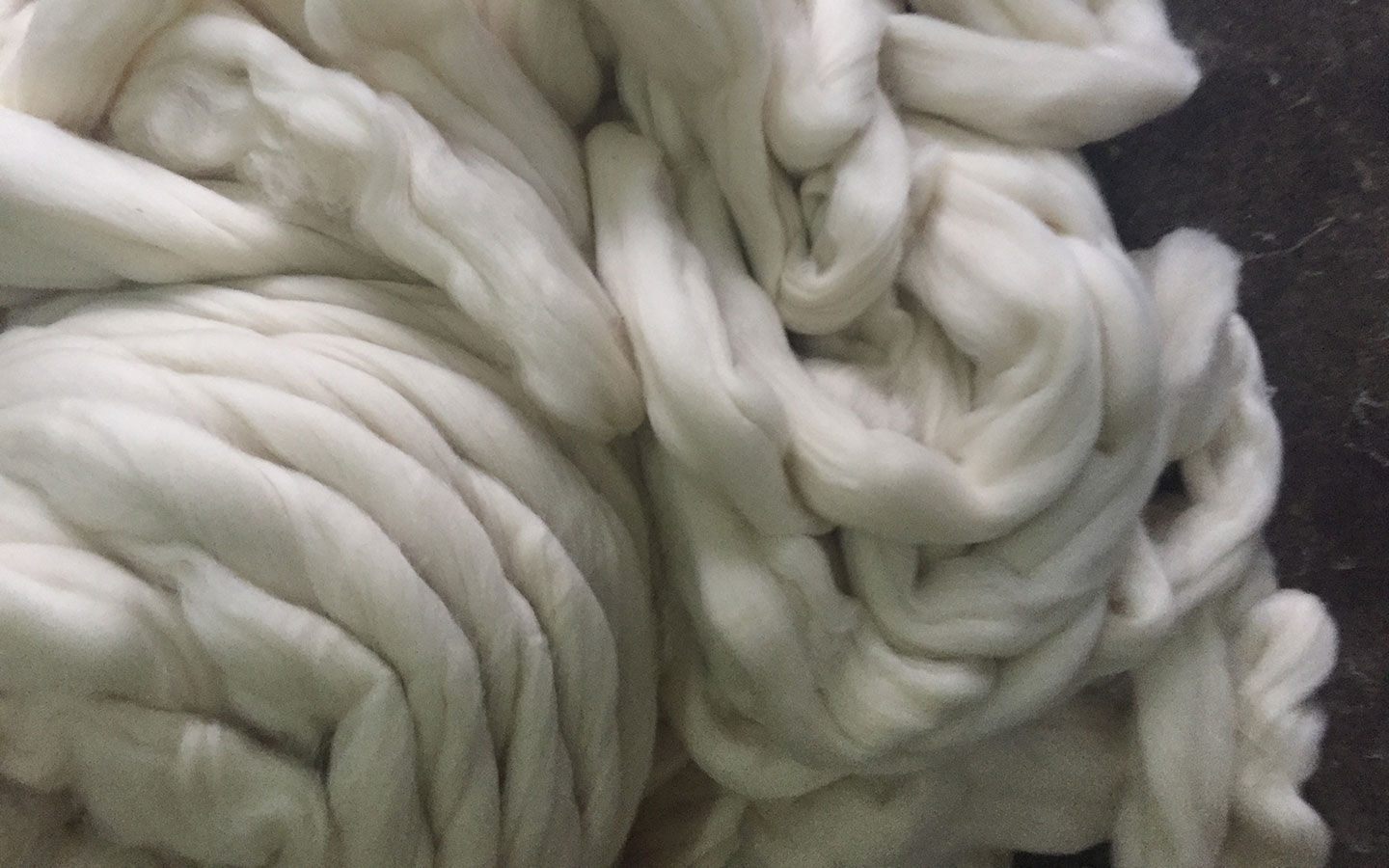
TOP MAKING
When wool fibre comes out of the scour, the fibres are in a random formation. The processes of carding (removing any remaining vegetable matter and dirt to open up the scoured wool fibres), combing (removing the short fibres and any foreign matters) and gilling (finer and more refined combing) are used to arrange the fibres in an organised and parallel form.
Once the Baggy Green wool was scoured and made into tops at Michell Wool it then went to Zhejiang Shenzhou Woollen Textile Co. in China for the next stage of processing.
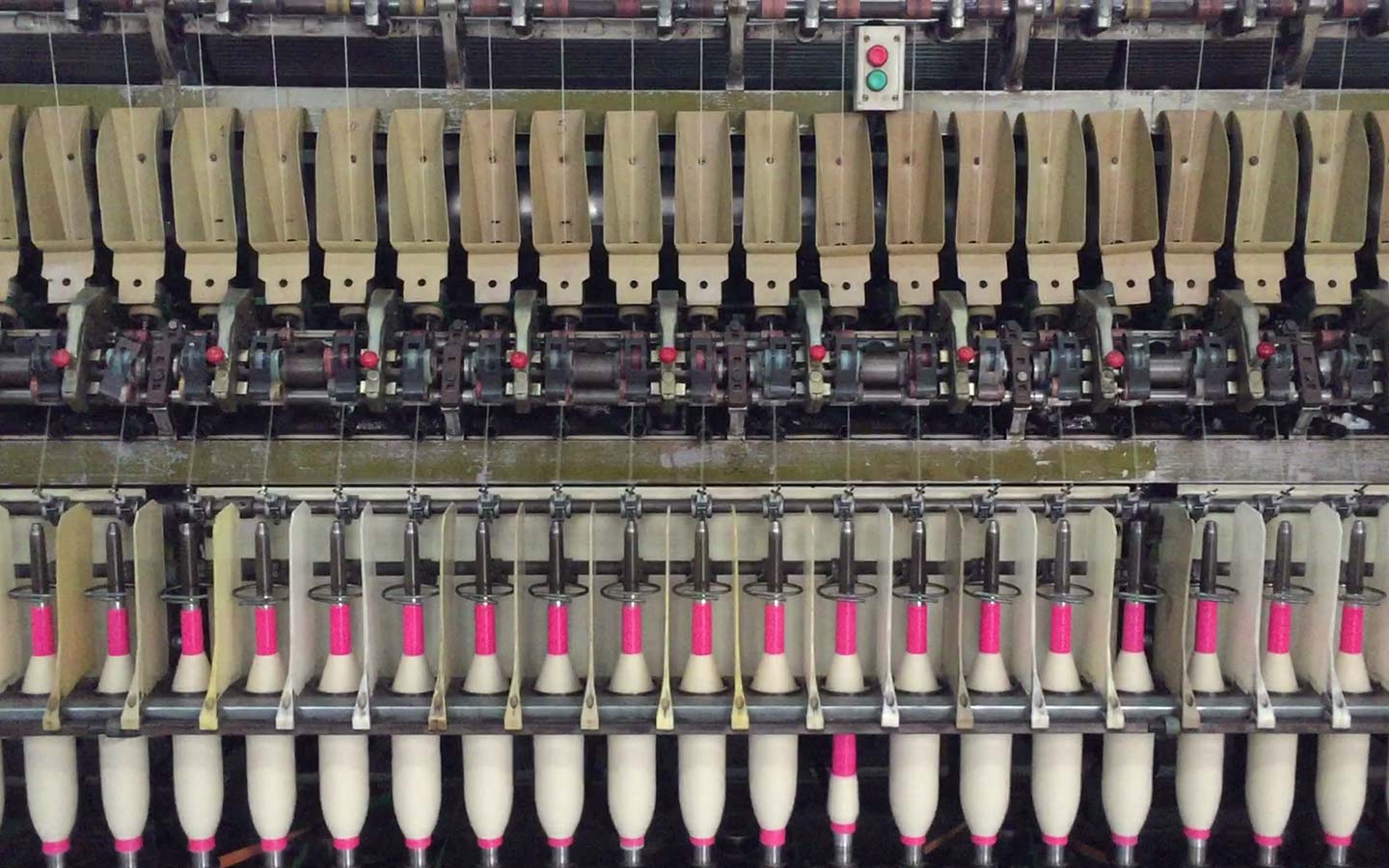
SPINNING
The Zhejiang Shenzhou Woollen Textile Co. were responsible for the next four stages of processing the Baggy Green fabric. Spinning is the process of inserting twist into assemblies of fibres (in top form) to make yarns. There are three common types of yarn in the wool industry, woollen yarns, worsted yarns and semi-worsted yarns. The Baggy Green wool was processed into a woollen yarn, characterised by the hairy, shorted fibres. After twisting, the yarn that formed the Baggy Green fabric was re-wound onto suitable packages ready for weaving.
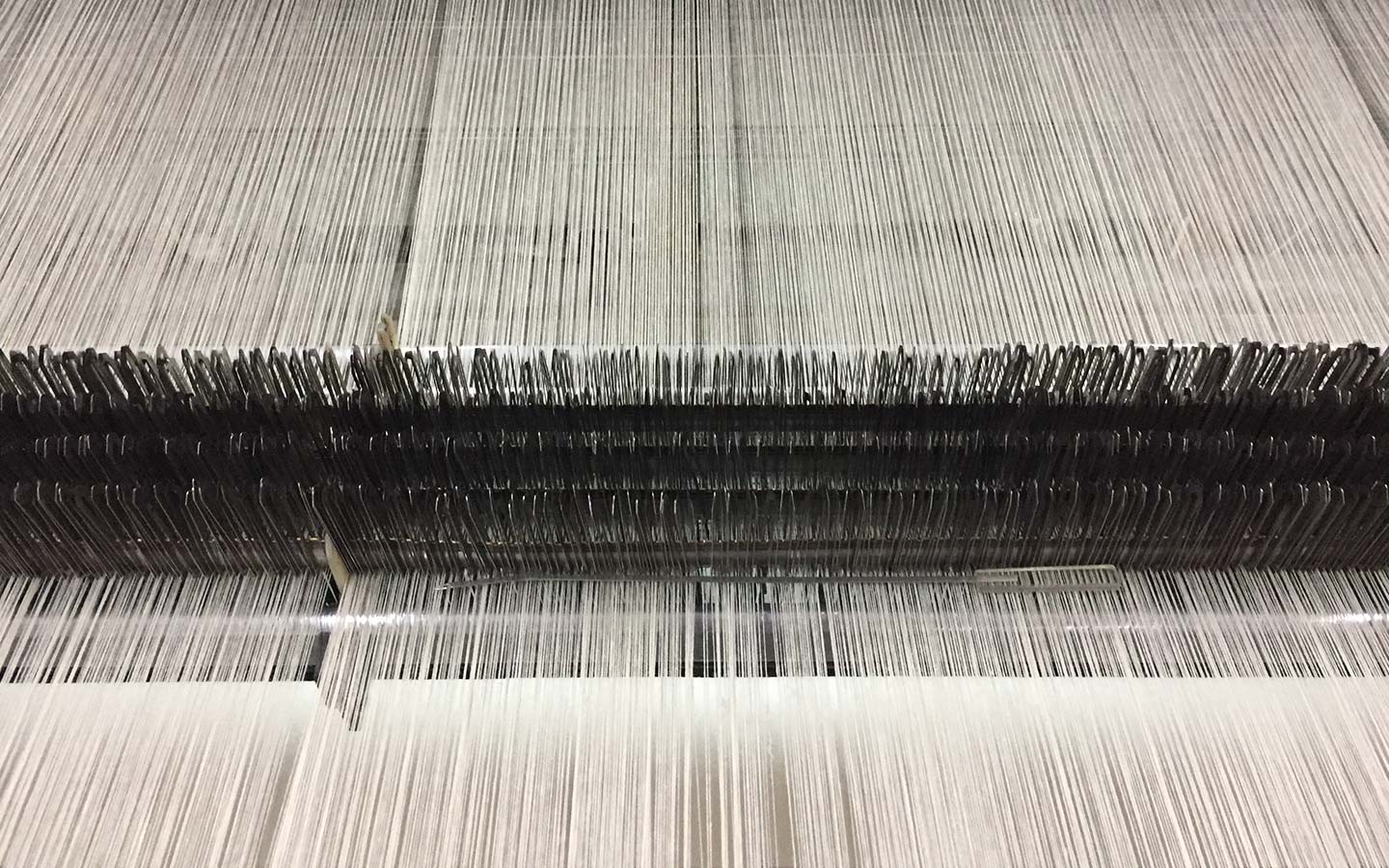
WEAVING
Weaving is a process whereby woven fabrics are formed on a loom by the interlacing of warp yarns which are set length ways on the machine, and a weft yarn is inserted usually at right angles to the warp.
During the weaving of the Baggy Green cloth, there were three primary motions:
• Shedding: where some of the warp yarns are lifted up to form a tunnel, where the weft yarn is inserted
• Picking: insertion of the weft yarn
• Beating up: beating the weft yarn, so it lies adjacent to the previous weft yarn.
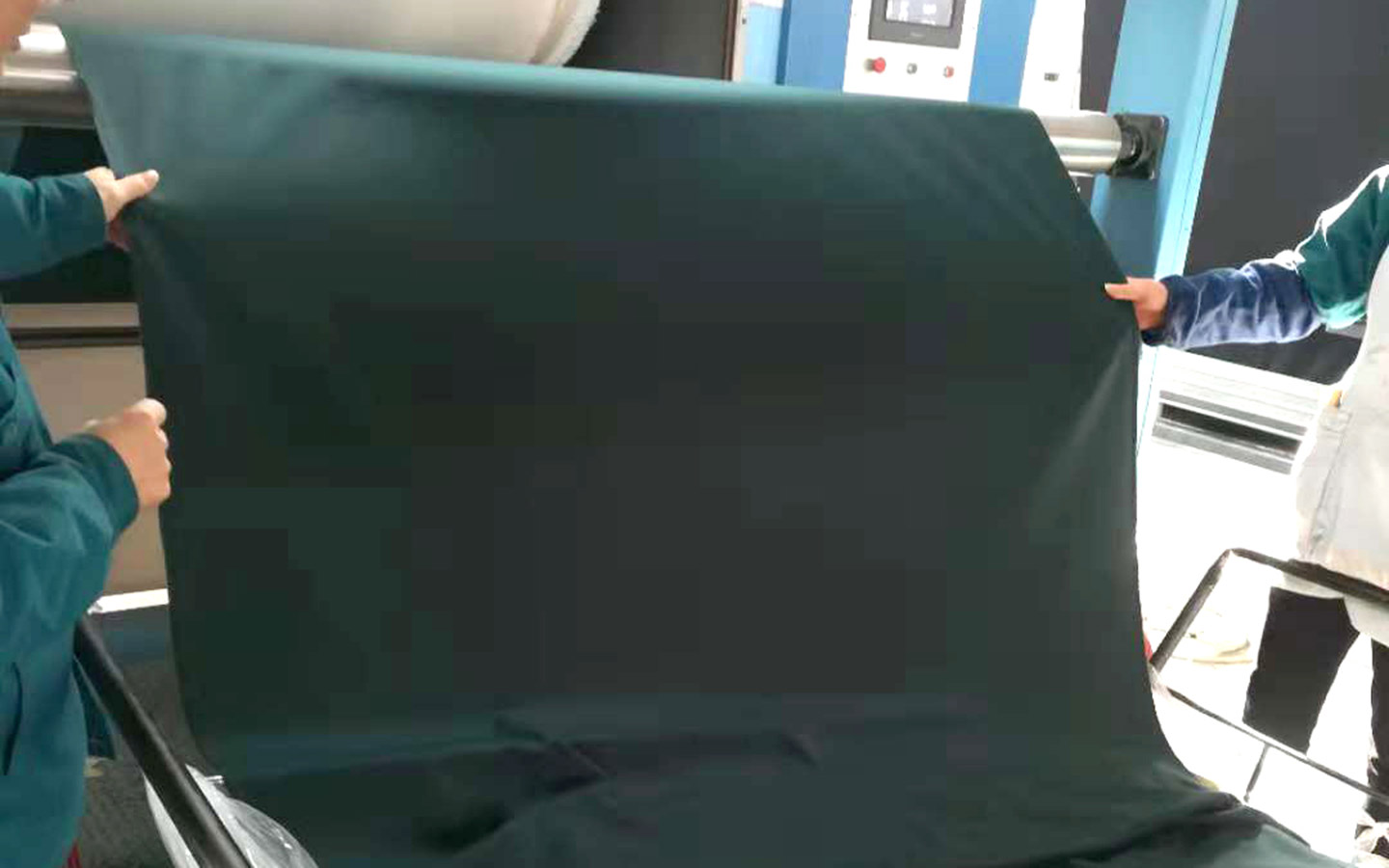
FINISHING
The finishing of woollen products usually comprises the following main stages: scouring, milling, rinsing, drying and dry finishing.
Both scouring and milling involves washing the fabrics in a controlled manner, in warm water containing detergent. Sometimes alkali is added to the solution to assist in better removal of processing oil.
The fabric was then thoroughly rinsed in clean water and dried and go through the dry finishing process such as decatizing for setting of the fabric.
The Baggy Green fabric will then be shipped back to Australia.
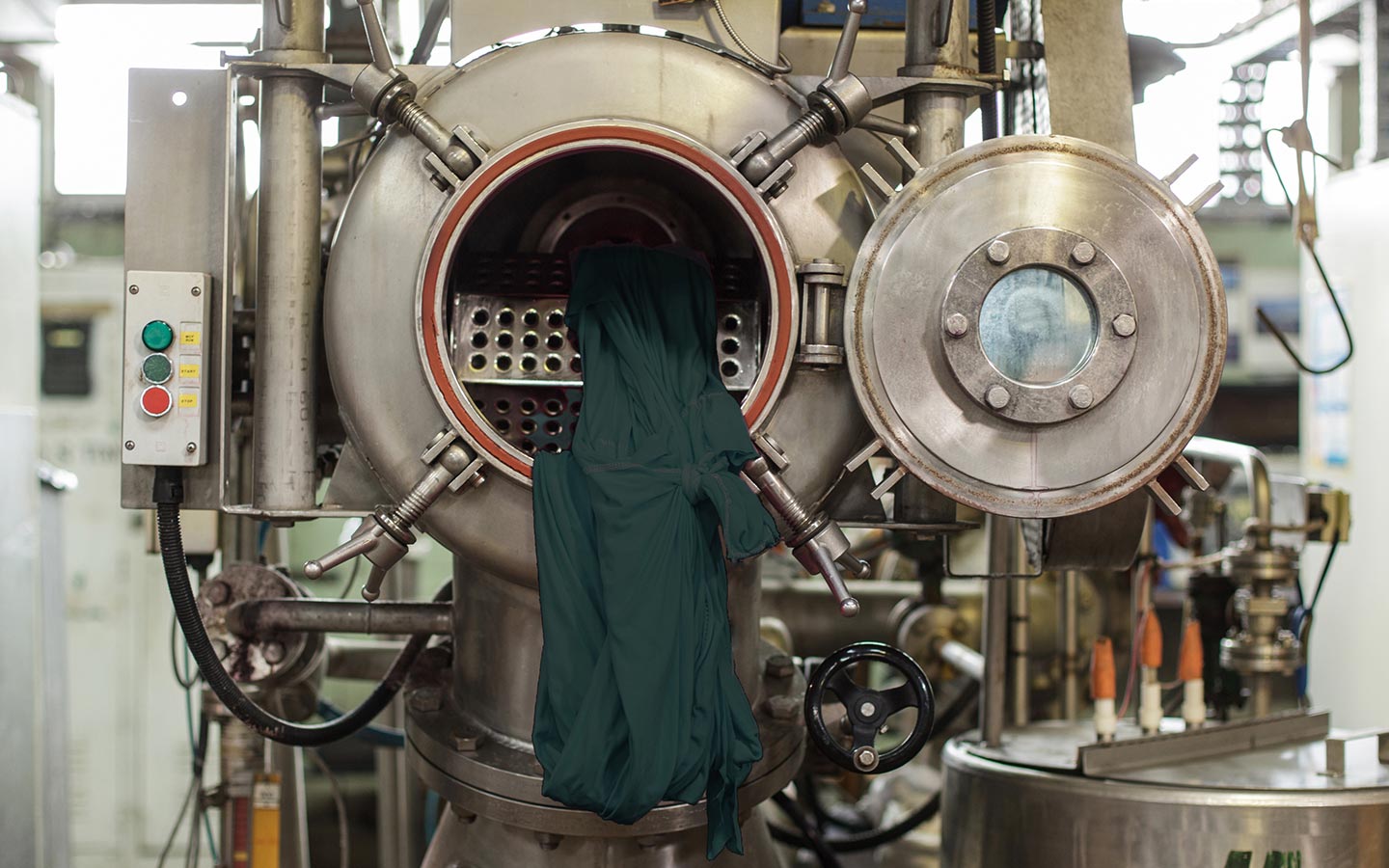
DYEING
The cloth was then dyed the iconic Baggy Green colour. Most dyes for wool are anionic (negatively charged) in their chemical nature, and the rate of dyeing is controlled primarily by controlling both the pH and the rate in the rise in the temperature of the dye bath liquor.
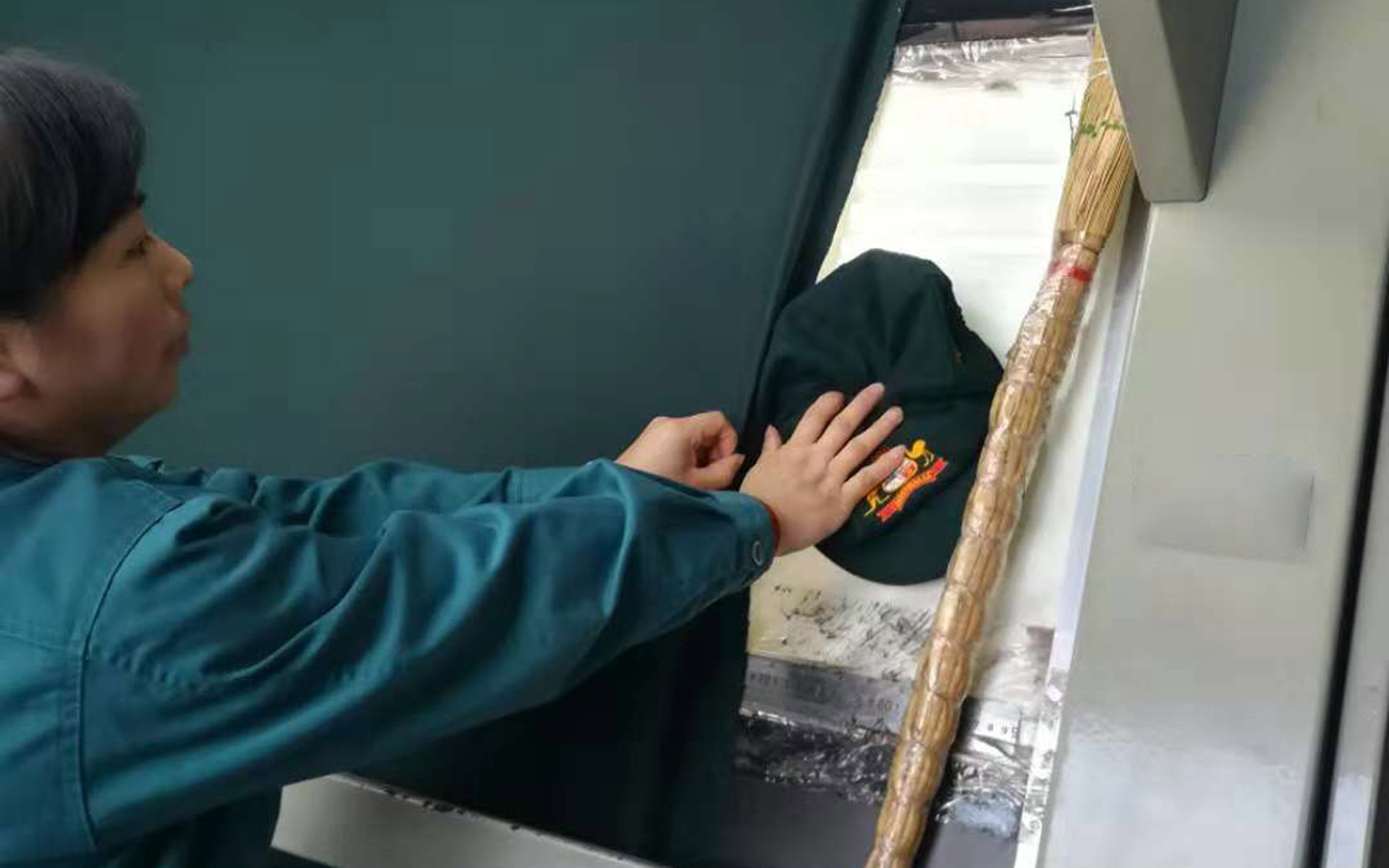
MAKING
The cloth will now be handed over to Kookaburra Sport for the making of the Baggy Green.
Kookaburra Sport was established in 1890 and is a 100% Australian family owned and operated global business. Kookaburra is the official uniform manufacturer for Cricket Australia and is charged with making each and every Baggy Green. To do so, individual panels are cut from flat fabrics and are sewn together to form the Baggy Breen. This process takes place in Perth.
The Journey Continues...
The cloth will now be handed over to Kookaburra Sport for the making of the Baggy Green.
Kookaburra Sport was established in 1890 and is a 100% Australian family owned and operated global business. Kookaburra is the official uniform manufacturer for Cricket Australia and is charged with making each and every Baggy Green. To do so, individual panels are cut from flat fabrics and are sewn together to form the Baggy Green. This process takes place in Perth.
In partnership with:
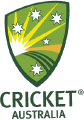
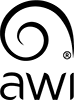
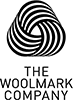
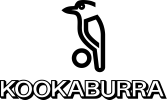