Wool workwear is a belter in the smelter
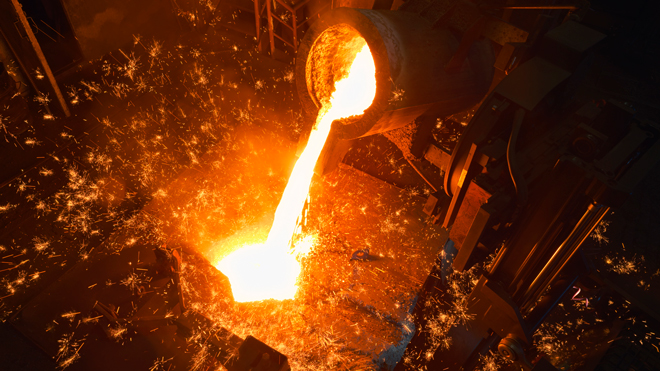
US company Burlington Fabrics uses Australian Merino wool to manufacture a commercially successful fabric that is not only flame resistant but also repels molten metal splashes. This is a good example of how wool is an ideal fibre for the protective workwear market.
In April, the Woolmark Americas team visited the Carolinas, a region well-known for textiles in the US, to have collaborative discussions with wool processors there on opportunities for growth in wool textile production stateside.
One of the companies visited was Burlington Fabrics, a leader in textile innovation and production for more than a century. It manufactures fabrics for markets including activewear, military, interiors, medical, and personal protective equipment (PPE).
Burlington’s BodyShield™ wool fabric
One of the many successful textiles that Burlington produces is BodyShield™, a fabric which is resistant to flames and molten metal. It is designed for PPE for people working in smelters, foundries, steel mills and aluminium plants.
Noriske molten metal resistant PPE made from Burlington Fabrics’ BodyShield™ wool fabric.
“The development of our innovative BodyShield™ fabric was initiated more than 25 years ago by a molten metal aluminum smelter in Canada, which identified a critical need for a lightweight, washable garment that not only possessed flame-resistant properties but also effectively sheds small splashes of molten metal,” said Bertrand Ross, Account Manager at Burlington.
“In response, Burlington collaborated with Woolmark to modify the Zirpro flame resistant treatment technology, tailoring it to fit our manufacturing processes. This adaptation ensured that our fabric would meet the rigorous demands of the smelting environment.
“Unlike traditional flame resistant fabrics, onto which molten metal can stick, our fabric allows liquids to roll off, ensuring safety and comfort. It proudly holds the highest ISO 11612 rating of D3/E3, guaranteeing exceptional protection.”
“With more than 25 years as a trusted choice for some of the largest smelters in the industry, our BodyShield™ fabric made from Australian wool has proven its worth time and again. Its blend of comfort, durability and protection has made it a staple in the workwear market.”
- Bertrand Ross, Burlington Fabrics
Bertrand says another key benefit of wool for workers is its ability to adapt to temperature changes.
“Whether it's a chilly winter day or a hot summer afternoon, Merino wool keeps workers comfortable by regulating their body temperature. Additionally, it effectively manages moisture, absorbing sweat without leaving them feeling damp – a critical feature for those facing demanding work conditions. Plus, it offers impressive durability with increased tear strength,” he said.
“We source 100% wool tops from reputable suppliers in Australia, a country known for its exceptional Merino wool quality, which ensures we use only the best materials.”
Sustainable sourcing and manufacturing
By prioritising eco-friendly materials and processes, Burlington ensures its fabrics not only perform exceptionally well but also have a minimal environmental footprint.
“Our use of 100% Merino wool means that when the fabric reaches the end of its life cycle, it naturally decomposes, leaving no harmful residues behind. PFAS, ‘forever chemicals’, have never been part of our production process for the BodyShield™ fabric meaning it is a safe and reliable choice for workers looking for effective protection without harmful chemicals,” Bertrand said.
“Our commitment to sustainability is also reflected in our manufacturing process; all steps – from spinning and weaving to dyeing and finishing – are carried out in our US facilities. This allows us to closely monitor our operations, reducing waste and minimising our carbon footprint.”
Commercially available products
Noriske molten metal resistant PPE made from Burlington Fabrics’ BodyShield™ wool fabric.
Burlington collaborated with its garment development partner, Noriske, during the original development of the BodyShield™ fabric, a partnership that continues to this day to create functional and durable solutions that prioritise worker safety and comfort.
Founded in 1982, Noriske is a 100% Canadian company that is specialised in producing high-quality PPE for optimal protection against splashing and radiant heat from molten metals. Its customers in this sector include large companies such as Rio Tinto and Alcoa.
“Noriske produces a large variety of products with the BodyShield™ fabrics including shirts, pants, vests, winter jackets, balaclavas and pitcoats. We offer more than 100 different items in this specific wool for the molten metal industry,” said Noriske Business Development Director, Raphaël Côté.
“The high quality, durability and general comfort of the fabric are key reasons for us choosing it. Wool is great for the temperature variation. In the molten metal industry, as you can imagine, the environment can be very hot and wet. The natural properties of the wool gives the wearers more comfort in a changing environment, as it will dry quickly and stay cooler in general.
“We have been supplying products made from these wool fabrics to customers for more than 25 years and we have no intention in changing a great recipe.”
Burlington’s new developments with wool
Burlington is expanding its Merino wool product offering with products that meet the needs of other markets.
“We’re dedicated to continuous innovation in fabric technology. Recently, we launched a new BodyShield™ blended fabric that not only delivers superior molten metal splash protection but also incorporates enhanced safety features, including arc flash protection and improved welding protection. These advancements ensure optimal safety for workers exposed to diverse hazards in industrial environments,” Bertrand said.
“Looking ahead, our focus is on developing a range of versatile fabrics that meet the specific demands of various applications. This includes next-generation materials engineered for the Canadian military, prioritising both durability and comfort under challenging conditions. Additionally, we aim to create next-to-skin knitwear featuring advanced wool blends, designed to provide exceptional thermal regulation and moisture management, thereby enhancing overall wearer comfort and performance.”
MAIN PHOTO: simonkr
This article appeared in the December 2024 edition of AWI’s Beyond the Bale magazine. Reproduction of the article is encouraged.