Wool Harvesting Innovation
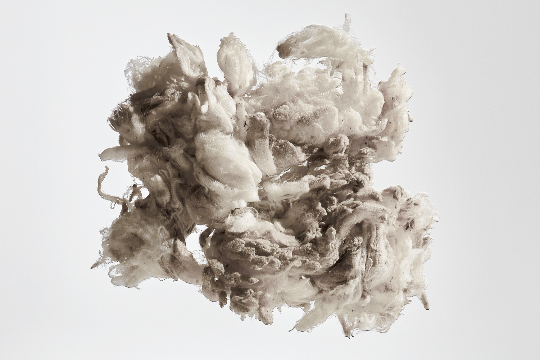
AWI invests in wool harvesting technology to improve workplace safety, animal welfare, boost clip quality and encourage new entrants into the industry.
AWI invests in wool harvesting technology to improve workplace safety, animal welfare, boost clip quality and encourage new entrants into the industry.
The biological harvesting project is critically important for the industry because we need to provide growers with new harvesting options.
Fully or semi-autonomous wool harvesting can access off the shelf robotics equipment and machine learning algorithms and adapt them to the various stages in the process from sheep delivery to a shearing position through to isolating black wool from the fleece and baling wool.
Artificial Intelligence technology can be developed for automation at any point along the wool harvesting process.
Biological Wool Harvesting
AWI is funding promising research into a new opportunity for biological harvesting of wool.
A new AWI-funded project with the University of Adelaide is investigating a new way of biological wool harvesting that enables the fleece to remain on the sheep, without the need for nets, until the wool is mechanically removed.
Previous attempts at biological wool harvesting concentrated on temporarily stopping wool growth, which resulted in fleece shedding. In contrast, the new approach is aimed at creating a weakened zone of wool. Previous trials showed that the fleece does not break off the sheep into the paddock under normal grazing conditions for up to ten weeks after the treatment was administered. Wool will continue to grow beneath the weak point, so as to protect the sheep from hypothermia and sunburn after the fleece above the weak point is harvested.
This new project will look at administering the treatment via an injection, rather than via feeding where there is the potential problem of ‘shy feeders’ not receiving a sufficient dose, and also differences in gut function between sheep.
Compared to traditional shearing, biological wool harvesting will improve wool quality by eliminating skin pieces, second-cuts (thereby resulting in even fibre length) and creating slightly reduced fibre diameter at the tips. Health and safety issues around sharp handpieces would be eliminated and animal handling injuries could be minimised through the use of upright platforms or conveyor belts.
AWI Biological Harvesting Day
Modular sheep delivery unit to eliminate catch and drag
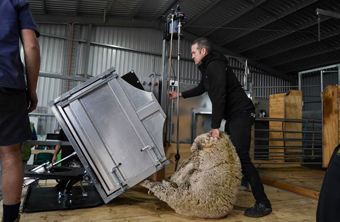
As part of a new AWI project, a mechanical system is under development that delivers the sheep to the shearer, thereby reducing the catch and drag. This minimises the chance of injury to the shearer and the sheep whilst also maximising productivity with significantly reduced handling times.
Robotic Assisted Shearing Scoping Study
The project has successfully used robotic technology to mimic the movements of shearing along the body of a life-size 3D printed sheep.
Current and Recent Projects
DEVELOPMENT OF SMART HANDPIECE
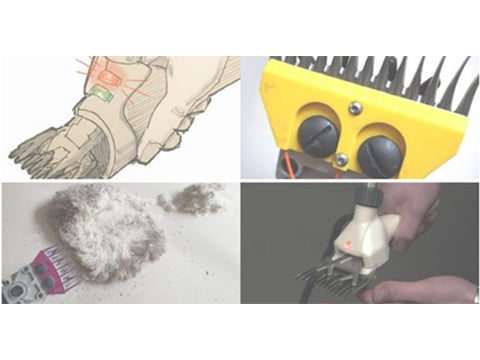
AWI is working with 4c Design (Numnuts®) to develop and construct a prototype of a smart shearing handpiece. The new semi-automated handpiece has the potential to make shearing available to less experienced operators while increasing animal welfare.
During the first phase of the project, 4c carried out extensive research in consultation with the industry, both in the UK and in Australia, to understand the current limitations of the handpiece and to identify which aspects can be improved to achieve these objectives.
The research team worked to enhance the comb and cutter integrating sensors to alert the user when either the tail or the nose of the handpiece is lifting to reduce second cuts and skin cuts. This feature will contribute to improve animal welfare and increase the quality of the clip.
They also explored the feasibility of a modular assembly removing the reliance on the downtube and wall-mounted motor. The user would instead wear a belt (for example) with power and drive for the handpiece providing total flexibility of movement to the shearer.
This motor and power system used to drive the device could also indicate that the gear is blunting and requires maintenance. Using sharp gear makes the job easier and knowing when to change the combs and cutters can take years of experience.
The second phase of the project aims to bring this technology to a development stage where a demonstrable ‘looks like /works like’ prototype that functions in the intended environment to desired performance, increasing the likelihood of commercial partners engagement.
Phase one: Development of a Smart Shearing Handpiece Final Report
Robotic Assisted Shearing Scoping Study
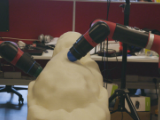
This project was a scoping study to develop a comprehensive understanding of how modern robotics technology could work within the shearing profession.
Incorporating modern robotics into some elements of the process of shearing offers the potential to enhance the physical and mental wellbeing of both shearers and sheep. The robotic system is being designed to reduce some of the physical strains and risks when shearing, including shearers being bent over for extended period of time creating strain on the back, and instead allowing the shearer to work in a safer and comfortable more upright position.
The project has successfully used robotic technology to mimic the movements of shearing along the body of a life-size 3D printed sheep.
The next phase of the project will use the new knowledge of robotic technology and refine the software and hardware of the technology for commercial potential in the wool harvesting industry.
The use of a 3D printed sheep ensured no sheep were used in the testing of the prototype and therefore no sheep were put at risk of being harmed in the testing of this technology.
Electromyography Signals
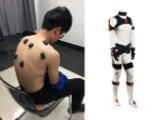
AWI is funding pioneering research to help shearers minimise back injuries through the use of wearable robotics.
Attracting and retaining shearers is one of the biggest challenges facing woolgrowers and the industry. A major factor is that shearing can be a ‘back-breaking’ profession, with injuries to shearers being six times the all-industry average in Australia. Lower back injuries are the biggest issue due to their long rehabilitation time and associated lost productivity.
A project funded by AWI aims to understand exactly how these injuries arise and then research potential wearable robotic solutions for shearers to reduce the risk of injury while still allowing the high degree of maneuverability required for shearing.
The initial objective of the project is for the researchers to accurately identify the mechanisms of lower back musculoskeletal injuries in shearers. With this knowledge, researchers aim to develop a practical and cost-effective prototype tool to be worn by shearers to alert them when they are becoming vulnerable to potential injuries. This sensing unit would propose optimal resting cycles and could potentially be connected to a mobile phone application.
By the end of this 12-month project, researchers will also develop a conceptual design for a more active solution for fatigue management and injury prevention, such as an exoskeleton that the shearer can wear.
The measurement platform will combine two separate sets of wireless sensors (pictured) to measure muscle activity and shearers’ body motion and posture simultaneously, allowing the study to take place inside shearing sheds instead of inside a lab.
A measurement system will be developed by University of Melbourne researchers for shearers to wear during the research. This system will monitor the shearers’ muscle activities and posture to estimate the potential injury.
The shearers’ measurements will be collected on a specially designed portable measurement platform that will be installed in a real shearing shed where it is possible for the shearers to shear more than 200 sheep per day. Researchers will therefore be able to study the shearers’ biomechanics in authentic conditions.
To understand the dynamics of lower back muscles under different shearing environments, factors that will be considered include whether or not each shearer has had a prior injury, the different skill level of each shearer (highly experienced or new to shearing), the age of each shearer and whether or not a back harness is used.
Innovative Shearing Industry Technologies
The Peak Hill Industries ShearEzy shearing system is a successful alternative to on the board shearing that eliminates the need to catch and drag sheep. The ShearEzy provides the shearer with a comfortable, stand up, working environment and meets the highest standards in wool preparation and shearer safety technology.
The ShearEzy is a product of AWI investment in Upright Posture Shearing Platform (UPSP) technologies. The product became commercially available in late 2007, with the most recent version released in June 2012. ShearEzy benefits include:
- Reduced physical effort and strain from shearing.
- Can be more productive than on the board shearing, especially for the novice or average shearer.
- Simpler blow patterns and effective animal restraints.
- Easy separation of crutchings and lower quality wools.
- Other animal husbandry tasks may done as part of the shearing process.
- Large sheep and rams are easily and safely handled without sedation. ShearEzy is an air-operated system, consisting of a shearing platform with an integrated parallel sheep loader. Sheep walk into the loader on an inclined, non-backup ramp and are confined until ready to be shorn.
The loader clamps the sheep then tilts and inverts the sheep placing it on the platform. The sheep can be crutched in this restrained position then released from the clamp.
To shear the sheep, the rear legs are restrained as the sheep lies horizontal between the hinged up wings of the platform. Rotating leg restraints and the hinged wings allow the shearer to mechanically manipulate the sheep to each desired position through the shearing process. Optimal flat surfaces for the shearer allow long continuous blows around most of the body of the sheep.
Heiniger EVO anti-lock technology attached to a balanced boom and flexible drive improves safety and productivity.
New features of the 2012 version of ShearEzy include:
- Reduced height and overall length.
- Better sheep flow due to sheep entering the machine at a lower level.
- Fleece removal from the side where the sheep is shorn, reducing space requirements.
- More adjustments both for the size of sheep and the operator.
- The main ShearEzy can be unit can be reduced to 1.8 metres long and 1.2 metres wide and is fitted with large solid rubber wheels to make it easy to move about, and roll onto a ute or trailer.
- A price reduction to $15,100 plus GST ex the factory. This includes the shearing plant and stand, and the non-backup ramp. An eight cubic foot per minute air compressor and handpiece are also required.
Further Information
See the Peak Hill Industries ShearEzy in action
Contact Bill Byrne at Peak Hill Industries (www.peakhillindustries.com.au) or call Bill on (02) 6869 1700.